Strength design of components
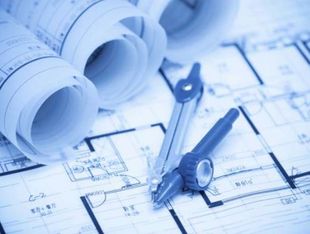
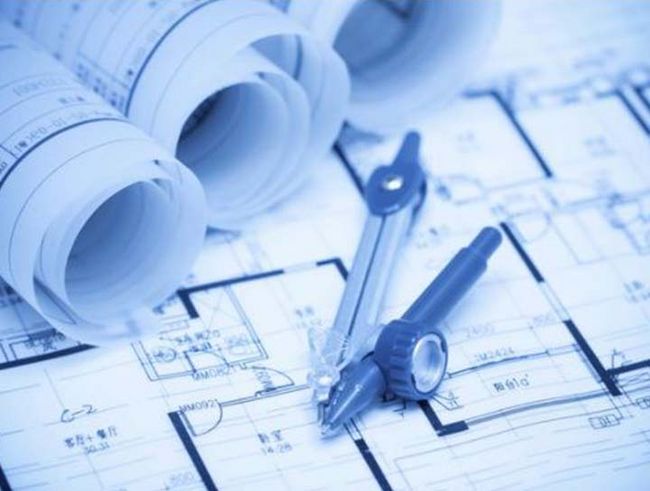
For power generation or nuclear safety functions a number of vessels, pumps, valves and piping is required. Beyond normal operation, components with safety functions have to fulfil their respective tasks during anticipated operational occurrences and accidents, which in turn, are either caused by external impact such as earthquakes or airplane crashes, or by internal events like component failure etc.
TÜV NORD Nuclear performs independent calculations to verify whether all applicable loads and load combinations imposed on the components can be accommodated, thereby ensuring the appropriate component function when required.
Our services
This includes reviews of the strength design of vessels exposed to dynamic loads due to e.g. earthquakes. Other issues are for instance computational analyses of the impact suffered from loads due to an airplane crash.
- TÜV NORD Nuclear uses the finite element codes ANSYS and ABAQUS for stress and fatigue analyses of complex component geometries.
- For preparing the finite element (FE) models, TÜV NORD Nuclear uses suitable CAD tools, such as CAE, PATRAN, DesignModeler or Autodesk Inventor.
- The ROHRII program is applied for piping calculations.
- For standardized components, such as supports, flanges, screws, etc. TÜV NORD Nuclear uses the Dimy program as well as own codes.
- TÜV NORD Nuclear uses the finite element codes ANSYS and ABAQUS for stress and fatigue analyses of complex component geometries.
- For preparing the finite element (FE) models, TÜV NORD Nuclear uses suitable CAD tools, such as CAE, PATRAN, DesignModeler or Autodesk Inventor.
- The ROHRII program is applied for piping calculations.
- For standardized components, such as supports, flanges, screws, etc. TÜV NORD Nuclear uses the Dimy program as well as own codes.
Leak-before-break analyses for piping and vessels are carried out using analytical and numerical calculation procedures. Furthermore, crack growth calculations for defective components allow for an estimation of their expected remaining service life.
The functional performance of valves is analyzed in the context of system assessments. For this, the closing behavior of e.g. valves and sliders is reviewed.